Behind the Project: Regent Century Park Condominium Water Feature Restoration
- Communications Entuitive
- Aug 6, 2020
- 5 min read
Updated: Nov 19, 2024
We sat down with David Sirois, a Designer based out of our Edmonton office, to talk about an interesting project he was a part of: the restoration of the Regent Century Park Condominium (RCP) Water Feature in Edmonton.

Thanks for sitting down with us, David. Tell us about this project.
David: RCP is a two building development in Edmonton featuring a landscaped area including a water feature between the two buildings, constructed above a continuous parkade. Entuitive was brought on to complete an assessment of the leaks into the parkade below, which were suspected to be coming from the water feature.
What’s unique about this project?
David: The complicating factor with the continuous parkade structure was that the portion underlying the landscaped area is not property of the condominium. Rather, that portion of the parkade is property of the adjacent tower, which was originally intended to be constructed as a part of the Regent Century Park condominium, but was delayed and completed as a rental apartment some ten years later, while the parkade serving it sat empty (except for the water that was getting in).
Over the course of the ten years that the RCP buildings had been operational, the water feature had worked for about 20 days, the original waterproofing and a secondary liner splitting that time. Based on our initial look, we quickly ruled out a plumbing problem.
After reviewing the base-building drawings, we did some exploratory excavation in the grassed area next to the water feature to review the condition of the structure waterproofing. What we found was that the waterproofing under the landscaping was actually in pretty good shape, and the drawings showed this waterproofing to extend under the water feature as well. The topping slab at one location in the water feature had been excavated previously and the membrane taken up to review the structure without reinstating the waterproofing.
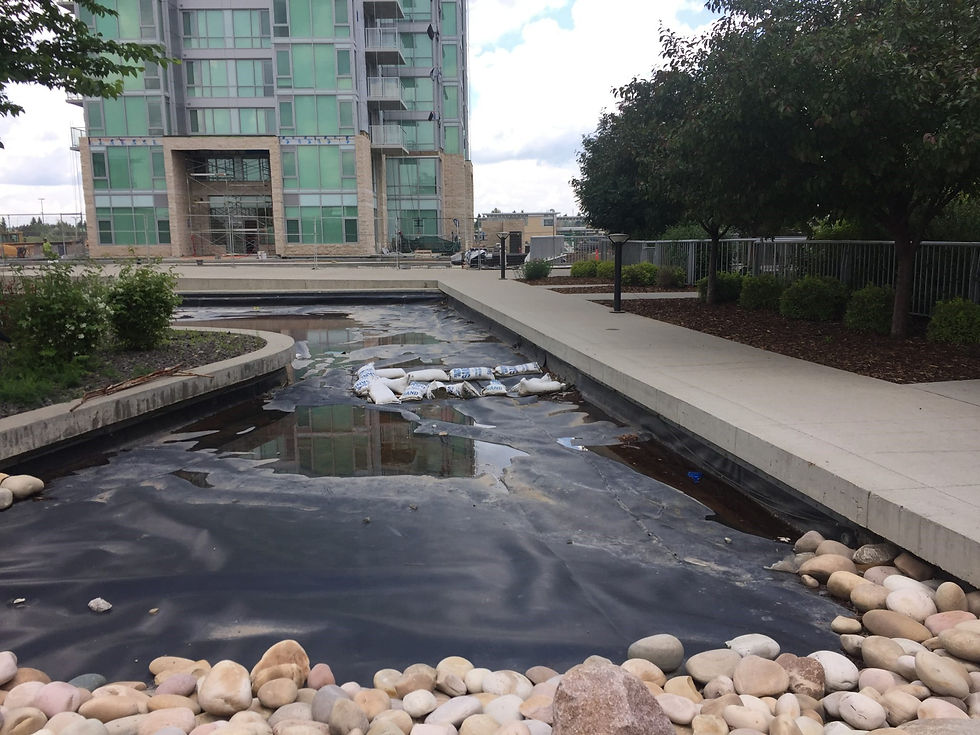
The good news about the compromised area in the water feature was that it gave us a really clear indication of what the original construction was to compare to the drawings that we had reviewed, and we could piece together the history of the water feature. Some of our investigating uncovered a few issues, including structure waterproofing that had debonded from the water feature perimeter walls due to UV exposure, inadequately sealed plumbing penetrations from previous liners and penetrations through the structure for electrical and irrigation services to feature areas inadequately sealed.
The time that we started our investigation to the time that the water feature needed to be up and running was approximately two and a half months, so while we were still piecing things together, the contractor who assisted with the exploratory investigation commenced demo of the previous liners. The condominium board of directors approved a concept based on sketches over the original drawings and an estimate for the contractor’s T&M costs, the contractor got to work.
To ensure that future performance of the structure waterproofing would not be compromised, we first had to step back, cutting out concrete around the whole perimeter of the water feature and excavating the soil in the island and peninsula features to repair the structure waterproofing.
Demolition completed, the water feature electrical ground grid was reinstated with properly sealed penetrations (and deleted penetrations where possible), concrete was placed back around the perimeter of the water feature, this time with walls extending up to the underside of the existing overhang to create a bathtub to protect the structure waterproofing against mechanical and UV damage. With the bathtub concept complete, a liner was ready to be installed to retain the water.
Because of the tight schedule, the new water feature liner would be installed to concrete placed only one day prior. It was impossible to use a fully adhered membrane due to loss of moisture in the concrete that would typically continue for up to 28 days, which would cause the membrane to debond. Instead, a local industrial liner installer was engaged to install a fabric reinforced polyurea liner that was brought to site in pre-manufactured sheets, with laps in the sheets receiving a field-applied coat of polyurea and the liner secured to the new concrete walls with a sealed termination.

While the construction work was ongoing above ground, the contractor was working underground with their plumbing and electrical subtrades to ensure that all of the water feature services were ready to fill and recirculate over 30,000 gallons of water when the time came.
In the end, the liner was completed at approximately 5:00PM on the day before the deadline, with a 24-hour cure time. I had the privilege of being on site on the Friday evening with the contractor to open the valves and fill the water. With a few minor hiccups, the water feature was once again operational. The water feature operated and retained water for the next 30 days before being closed for the winter. It was filled once again this past spring and has continued to perform as intended since that time.
What was your favourite part of this project?
David: This project drew on a very broad range of skills and knowledge throughout the firm. Once I knew what I was up against, I was immediately able to connect with colleagues in Calgary, Toronto and Vancouver for advice and validation on things like concrete bathtub water-retention structures and water feature liners that escape the conventional restoration and waterproofing wisdom. Being able to tap into the knowledge across borders was paramount in ensuring that we could arrive at a solution that was both creative and achievable given the tight time frame.
In addition to the internal collaboration, it was very rewarding to collaborate with the contractor, property manager and condominium board on this project. We did not physically have the time to tender the work for competitive pricing, so a trusting and transparent relationship between all parties was critical in order to get this done. Open communication was key – whenever a new problem came up on site I knew within minutes, and whenever I proposed a new idea it was quickly analyzed and evaluated on its merits and feasibility.
Any final thoughts?
David: This project is unmatched as a learning experience for things that don’t necessarily have a lot to do with engineering. At the outset of the project, we did not know what to expect, or what skills I would need to employ to get the job done, but by being adaptable and open to an unconventional approach to project delivery, we were able to meet the client’s needs, and getting there would not have been possible without the support from those across the firm who collaborated with me or the trust that the contractor and the client showed us as a firm to provide an effective solution and deliver on time.
To learn more about this project, reach out to David Sirois.
Comments