Behind the Project: FIS Headquarters
- Communications Entuitive
- Feb 24, 2022
- 5 min read
Updated: Nov 25, 2024
The new FIS Headquarters building in Jacksonville, Florida will provide a distinct presence and prominence along the St. Johns River for an expanding fintech company. Recently, we sat down with Associate, Timothy Wong to discuss the project in more detail.
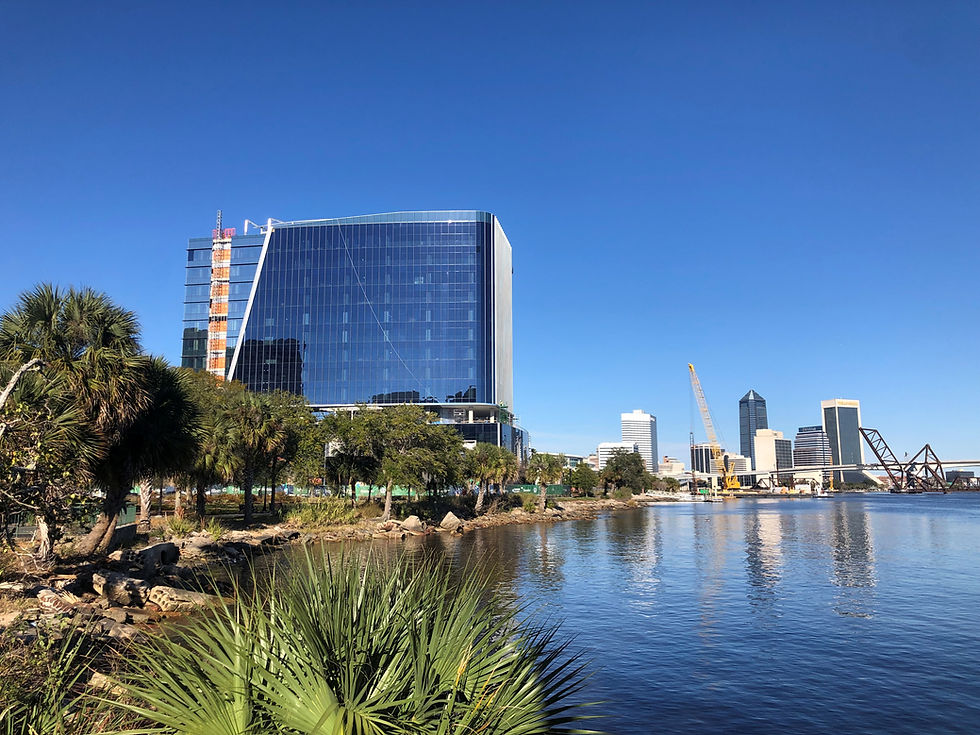
Thanks for sitting down with us today, Tim. Can you please tell us about the project?
Tim: The headquarters is designed as a twelve-storey tower with a distinct detached parkade. It will serve as the company’s home base after they consolidate their existing locations in the neigborhood. It’s a beautiful location, right on the St. John’s River. The building is set back into the landscape to help address potential flooding and sea level rise. There’s actually an article by Gensler on design climate-ready buildings with this project as the focus.
We were engaged by Hines and Gensler to serve as a building envelope consultant on the project from schematic design through to construction completion. A separate team is also providing the distinct building enclosure commissioning (BECx) scope for the development.

Sounds like a beautiful project. Can you share some of the unique aspects that you were involved in?
Fin Detailing
Tim: In terms of the envelope, there is a three-storey podium structure, followed by the main tower above. The main tower floors have a small floor plate then the podium, and the remaining areas of the podium roof create an accessible landscaped terrace. A unique part of the envelope are the distinct diagonal edges that run down each elevation. Given the edge is also sloped, this creates a unique articulation in the façade as if the thin veil of the curtain wall extends past and reveals the core at the corners. This is further highlighted by integrated lighting and the contrasting horizontal fins.
In terms of expression, there is a large fin projection, almost 3 feet wide off the face of the curtain wall. The team had to consider the dynamics of the wind pressure at corners to design the fin to resist added loading and eccentricity. The fin was post-installed in the field. Post-installation allowed alignment and configuration to happen on site and lessen risk of damage during transportation.
Fly-By Condition
Tim: At the rooftop, the curtain wall continues up and creates a fly-by parapet condition, extending past the roofline. This allowed the design to conceal rooftop equipment from view and create opportunities for signage and display, while also creating a unique and intriguing roofline termination for the façade.
To ensure a watertight transition, a stack joint was created by halting the system at the roof line. We then installed the next extension of the curtain wall fully on the exterior. To support this cantilever, additional steel structure is anchored and bolted to the roof. This arrangement provides a panel line reading that is suspended and outside of the weathered envelope but provides visual continuity of the system.

What’s been your favourite part of the project so far?
The Design Tim: I really enjoyed the design. The project is a custom unitized curtain wall system. With the added vertical cap fins at every mullion on the tower element, the verticality of the curtain wall is highlighted. From the exterior, you are drawn upwards which provides a unique contrast against the horizontal landscape and St. John’s River around it. The Collaboration
Tim: I also enjoyed the frequent collaboration between the design and development teams. There has been consistency in project managers across the board, ensuring familiar faces were present for consistent collaboration and communication. Gilbane, as the contractor has been very communicative throughout the process. They have been very active and responsive in terms of on site quality control and kept us in the loop throughout the process.
The larger project team has been based predominantly in Florida and Texas. The curtain wall is being manufactured in Texas and delivered to Jacksonville. We were able to utilize our own Calgary, New York, and Vancouver resources to stay nimble and service the project.

Navigating Covid and Virtual Site Reviews
Tim: We began this project before Covid impacted the industry and the project officially went into construction a few months into the pandemic. It was interesting to be part of that transition. Initially, we had planned to do in-person meetings and visits of course, but at various stages of the pandemic this was not possible. We were able to pivot by conducting several virtual site reviews and online workshop coordination meetings. Although we couldn’t physically participate in weekly review, we were able to adapt quite well as a team to keep communication lines live and connected.
We were able to take advantage of virtual site reviews and work closely with Gilbane. There are advantages to this type of review, particularly when we just need to collaborate on one detail or element. Given the ease of virtual reviews we ended up having far more discussions and reviews than we would normally schedule. As the building envelope installation was progressing, a simple phone call and teams/zoom meeting could occur same-day where we could readily review actions in 30 minutes or less. The contractor would guide us through what they were looking at and we could identify and talk through problems virtually and come to resolutions swiftly.
Virtual site reviews can never replace a full in person site review because there are certain instincts and observations which occur in person that naturally can’t occur virtually. You might also miss out on advantages that come from direct client/contractor interaction, collaborative discussions, and facilitating problem solving for things you might not have planned to review. That said, I do see virtual reviews happening more frequently because it does save time and can be sufficient for certain on site collaborations or complications. For example, if we know exactly what we need to look at, we can pair up the two types of reviews and save time, making the whole project operate more efficiently..
Any final thoughts?
Tim: I’d also like to highlight some of the performance testing and commissioning. It’s a custom unitized curtain wall and we worked closely throughout the early shop drawing review process with the manufacturer and contractor for the curtain wall to fine tune, revise, and improve details. We had the system fully tested for structural, air, and water performance. For such projects, the ability to simulate loads on a building that would be experienced day-to-day is a crucial and a valuable aspect to the function of the envelope. This type of performance verification is key when dealing with custom projects on complicated enclosure profiles. This is just a small step along the path of building envelope commissioning, but an important one.
With Entuitive’s hybrid role of both envelope consultant and commissioning provider, our team was divided up into the commissioning group and the consulting team which worked independently throughout the project from one another but collaborated on deliverables to ensure conflicts were identified and resolved to ensure a smoother process for the design and construction team. This process took away some question marks for the team, for example potential scenarios that often arise related to conflicting comments on a detail or material selection which can cause unnecessary delays. The process internally also allowed for team members to keep one another apprised of project progress so the client, architect, and construction team could provide updates to any of the team members. The entire team was quickly made aware of the status of the project and any forthcoming action items to be addressed.
Thanks for sitting down with us today, Tim. It was great to learn more about this impressive project! If you’d like to reach out to Tim, you can do so here.
תגובות