Behind the Project: Edmonton Kingsway Mall Sears Redemise
- Communications Entuitive
- Dec 3, 2021
- 4 min read
Updated: Nov 27, 2024
Mohammad Moayyed is a Senior Associate and Colby Thompson is a Senior Engineer. Both work out of our Edmonton office and have been key players on a recent project in the city: the Kingsway Mall Sears Redemise. Recently, we sat down with them to learn more about the project.

Thanks for sitting down with us today, Mohammad and Colby. Can you please tell us about the project?
Mohammad: Thank you. This project is a continuation of our work with Oxford Properties at the Edmonton Kingsway Mall. We had previously completed Phase 3, which included the redevelopment of the south portion of the mall. In this phase, we are redemising the former Sears store building on the north side of the site. Walmart will be the anchor tenant, leasing the majority of the building’s two floors. In addition to this base building project, Entuitive is also collaborating on tenant fit-out scope with Walmart’s project team.
Colby: We are preparing and upgrading the space to meet floor loading and building performance requirements. The building is two-storeys, with one storey below-grade. During the design phase, we identified some issues with respect to the building’s age that we also had to address.
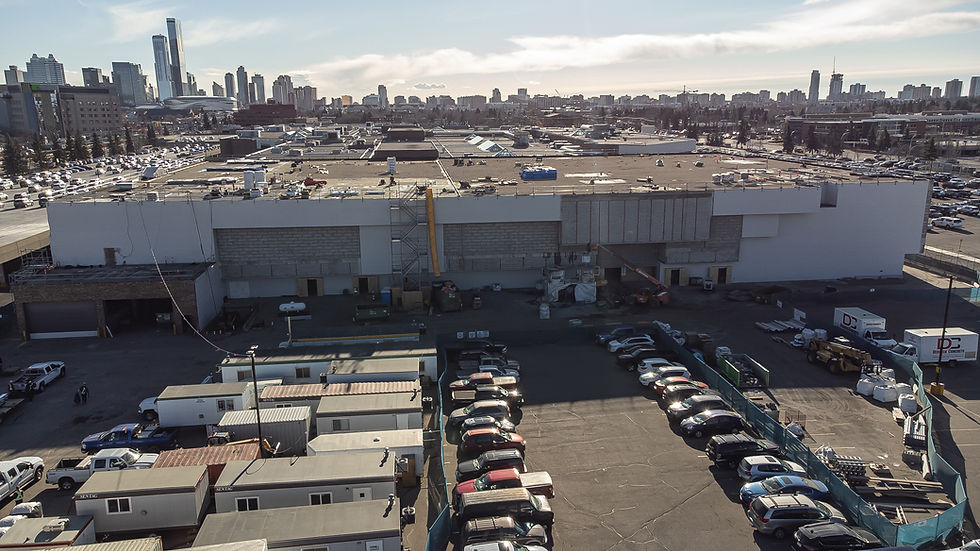
Oh, interesting. Can you please expand on some of the challenges that you faced?
Colby: Sure. I think the best way to discuss the challenges and solutions would be to break them down by area of the building, as it’s quite a large job site.
Basement & Level 1
Mohammad: I agree. One of the first challenges we had to overcome was the lack of existing drawings, which meant we didn’t know things like the structure’s load capacity, or the foundation and soil bearing capacity. So, one of the first things we did was a sequential exploratory investigation to collect as-built information. In collaboration with Oxford, ABBARCH (Prime Consultant and project Architect), and Ledcor (Project Construction Manager) various techniques were used for collecting this data, such as GRP scanning, surveying, coring, material testing, selective demolition, 3D laser scanning, and geotechnical investigation. We also developed an as-built 3D model to facilitate design team collaboration. The work allowed us to evaluate several possible approaches to optimize reinforcing scope.
Colby: We used an advanced finite element analysis, or “stage modelling”, to assess the existing floor slab’s structural behaviour and determine the optimum reinforcing design for strength and serviceability requirements. We utilized and combined various methods for structural strengthening based on the existing condition and new capacity demand. We added steel beams underside the slab, reinforcing existing columns by steel straps jacketing, new columns and new footings to help over loaded footings.
We also collaborated closely with the construction team to create a procedure for the development of a steel fabrication model based on the existing condition. Every beam is uniquely fabricated based on the existing slab geometry. The level of complexity faced by the construction team was sizable.
Entuitive’s team and LEDCOR’s team toured the site and explored some of the work they collaborated on, sharing insights with the broader team.
Roof
Mohammad: Some of the challenges at the roof area were that a full mechanical system upgrade required the installation of several large size roof top units. Additionally, the new tenant required new units which must be installed on the roof. We also faced existing ponding issues due to excessive slab deflection and the need to create new penetrations for the duct works.
Colby: To address these challenges, we determined several iterations for the mechanical unit layout to optimize the reinforcing considering required spacing between units, duct penetrations, roof slab geometry (e.g., opening in drop panel), and safety distance from the roof edge.
In the end, we stacked the units in the area of the roof where the structure below is being reinforced with extra capacity to carry new roof load condition. This also allowed us to locate the units in an area that minimizes snow drift, as required per the current Building Code.
The design team decided to add new roof drains and rigid insulation to solve the ponding issue, instead of costly roof structure reinforcing.

Temporary Shoring at the Escalator
Mohammad: The construction team faced a challenge in that there was no way to access the basement for material handling. This would have been particularly difficult during the excavation phase and taking the heavy steel elements into the basement.
Colby: To solve for this, Ledcor proposed a gantry crane which is installed on the main floor utilizing one of the existing floor openings. Our team provided the construction engineering services to Ledcor for review of the proposed system and temporary shoring of the existing structure for the crane installation. This is a great example of collaboration by the engineering and construction teams to find a solution that significantly improved the construction efficiency.
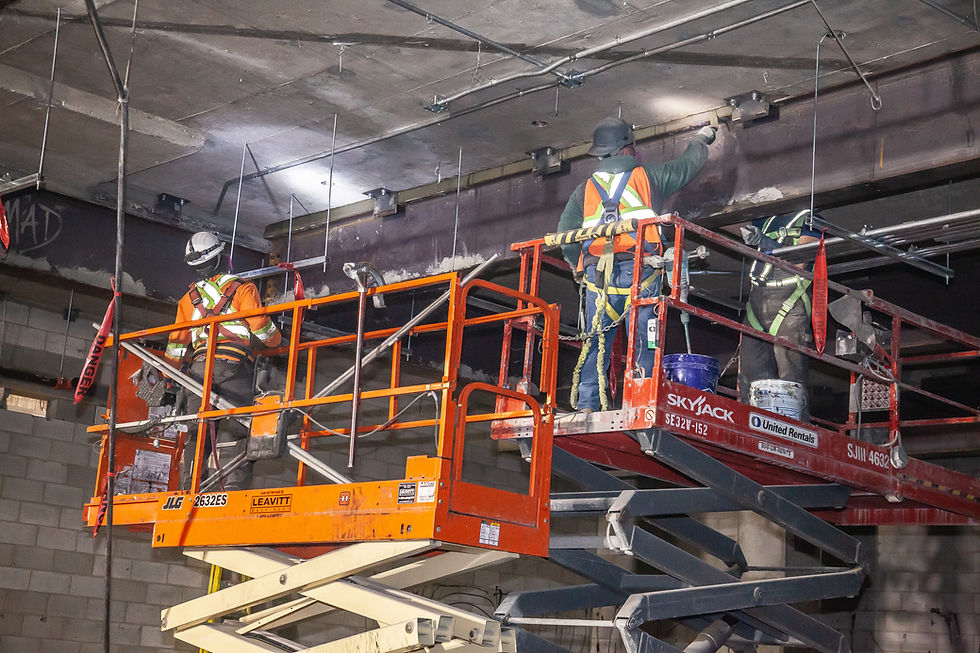
What has been your favourite part of the project?
Mohammad: I’ve been involved in this project since October 2017. It’s hard to pick a favourite part in a project with this scale and complexity. For me, the best thing will be when the project is handed over to Oxford on time and under budget, which I believe it will be the case here.
Colby: Using Stage modeling for existing structure reinforcing is my highlight on this project. It showed how Entuitive’s team can use advanced technology to provide best results for the client. It was a true example of Uncompromising Performance.
Thanks for sitting down with us today! We learned a lot.
If you’d like to continue the conversation, you can reach out to Mohammad here.
Comments