Behind the Project: Baird Blackstone Building
- Communications Entuitive
- Jul 28, 2021
- 4 min read
Updated: Nov 27, 2024
The Baird Blackstone Building (formerly Guildford Place) is a six-storey, timber-framed modular housing development in Surrey, British Columbia, Canada. The project is developed by BC Housing and will be managed by Lookout Housing and Health Society to provide permanent supportive transitional housing to those at risk of homelessness.
Recently, we sat down with Associate Timothy Wong and Building Performance Analysis Lead Tristan Truyens to learn more about the project.

Thanks for sitting down with us today, Tim and Tristan. Tell us about the project.
Tim: The Baird Blackstone Building is a housing project that is nearing completion this summer in collaboration with ATCO’s Permanent Modular Construction Division and Ron Hart Architects. Its purpose is to increase supportive housing stock in the province. Adjacent to an existing low barrier shelter, the building brings 60 new permanent studio apartment units and 24/7 support for people who are experiencing or who are at risk of homelessness.
Modular construction was a key component for the scale, function, budget, and schedule criteria on the project. This also allowed efficiencies for the modular builder based out of Alberta to implement quality control procedures in the factory and deliver fully finished and stackable units to the field.
Tristan: Because this is a BC Housing project, it had ambitious energy targets. There was a requirement to meet Step 3 of the BC Energy Step Code. The project had some aspects that made this more challenging than a traditional residential building, including a commercial-grade community kitchen and dining area on the ground floor, which presented quite a high ventilation heating and cooling load.
What were some of the biggest challenges you faced on the project and how did you solve them?
Waterproofing
Tim: One of the biggest challenges was related to the waterproofing component. We worked closely with the modular builder to develop processes and sequencing that are typically temporary construction practices such that permanent construction performance was achieved. This was important for both the transportation and construction phases, when the modules could be fully exposed to the elements for prolonged periods of time prior to arriving and being stacked on site. We designed with the understanding that some of what would protect the structures temporarily during transportation and construction had to be left in place. Of course, this also meant we had to approach the project holistically once assembled, given that between every module a construction joint was created that would need to be sealed, insulated, and clad.
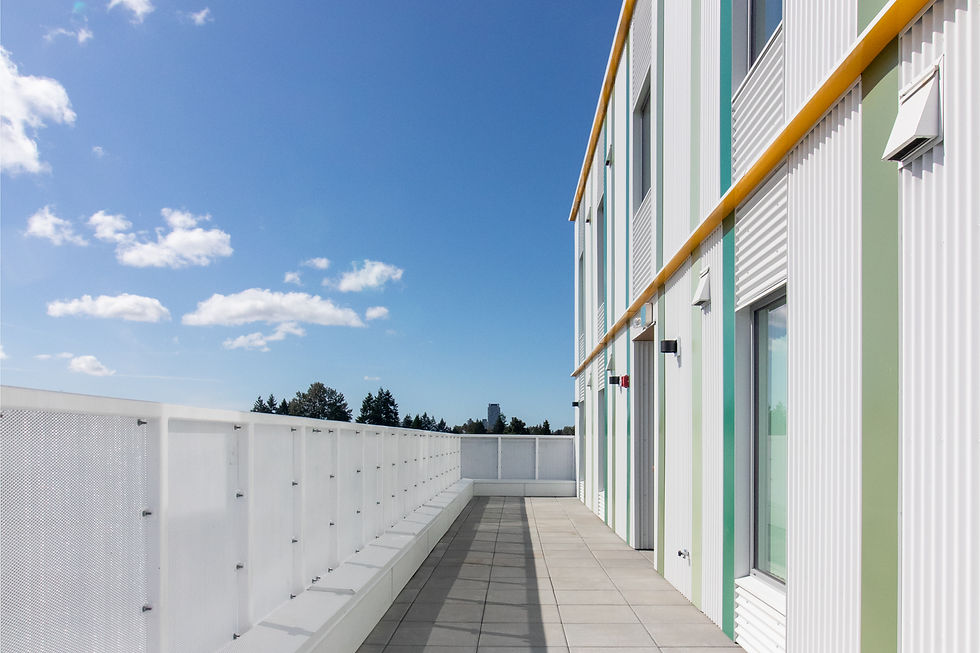
Energy Modelling
Tristan: From an energy modelling point of view, one of our biggest challenges was helping the design team to meet the high calibre energy performance requirements on budget. For instance, when we were first engaged on the project, there wasn’t an intention to provide cooling to the suites. However, because of the potential for vulnerable populations to be housed in the suites, we found that they needed to have cooling to meet the requirement of less than 20 heat stress hours a year set by BC Housing. With this understood, there was now an additional mechanical system that had to be added to the project.
It was important to work with the design team to help identify “state-of-the-shelf” equipment that could meet the high energy performance requirements set by BC Housing. This is where the integrated approach between Entuitive’s Building Envelope and Advanced Performance Analysis teams paid significant dividends. A good building envelope is a low-tech way to help maintain good energy performance without necessarily relying on high end systems.
Cladding Connections, Seismic, and Lateral Stability
Tim: Related to energy performance was the challenge that came up around cladding connections. At the onset of construction, we had to evaluate our methods of anchoring the cladding back to the structure in order to stay within schedule and budget. We had initially proposed using a thermally broken clip system but had to consider alternative options to secure the cladding to the building. We worked with Tristan to verify compliance, and at the end of the day, ended up finding a solution that was easier to procure, simpler to install, and improved baseline performance for our specific wall assemblies.
One last unique aspect, at six-storeys, this project is one of the taller modular projects in BC, so the approach to seismic and lateral stability was additionally accounted for by the design team. This created some unique detailing conditions that were mitigated as they relates to the thermal bridging impact on the insulated envelope.

What was your favourite part of the project?
Tim: I enjoyed the fact that the design team of consultants and development team were thoroughly engaged. Everyone was very responsive and the design accommodated practical approaches to the program of the building, the envelope, and the energy model.
Being active on site and able to see the progression, I believe it is a very welcoming space. The building has wide windows, lots of daylight, and the communal spaces have tall ceilings, contributing to the openness. This approach to occupant comfort is crucial to housing projects in general but even more so in a supportive housing project. I am glad we could contribute to the team and help develop a façade that was light, durable, and cost effective.
Tristan: Tim’s right, the design team were really a good group. Everyone was so effective and sensible. It was a very collaborative team. I’m really glad to hear it’s turned into such a lovely space, too.
This was one of the first projects that the (at the time) newly minted Advanced Performance Analysis team were engaged on, so it definitely has a special place in my heart.
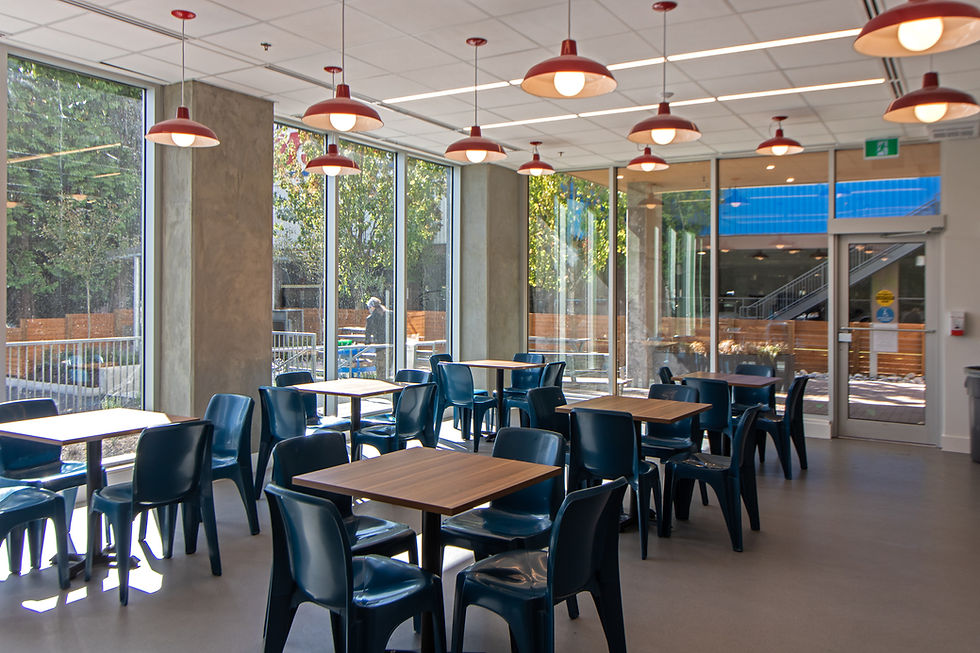
Are there any final thoughts?
Tim: This was a case where our One Company philosophy came into practice. I’m in Vancouver, Tristan is in Toronto, and we had boots on the ground at the fabrication plant from our Calgary office team. Tristan, Paul Creighton, and I were heavily involved with the design team – the builder, the architect, and their consultants. At the modular unit fabrication stage, air tightness and water tightness testing were performed for a mid-construction quality assurance. David Leonard and Saioa Biritxinaga led this effort. Tristan and Hamid Reza Hooshangi actively managed design iterations through to design, tender, and, ultimately, Negar Mozafari and I are seeing the project through to completion.
Thanks for sitting down with us today, Tim and Tristan. It was great to learn more about this project.
Tristan: It was a good experience working with all the offices throughout the project. One Company FTW!
Comentarios